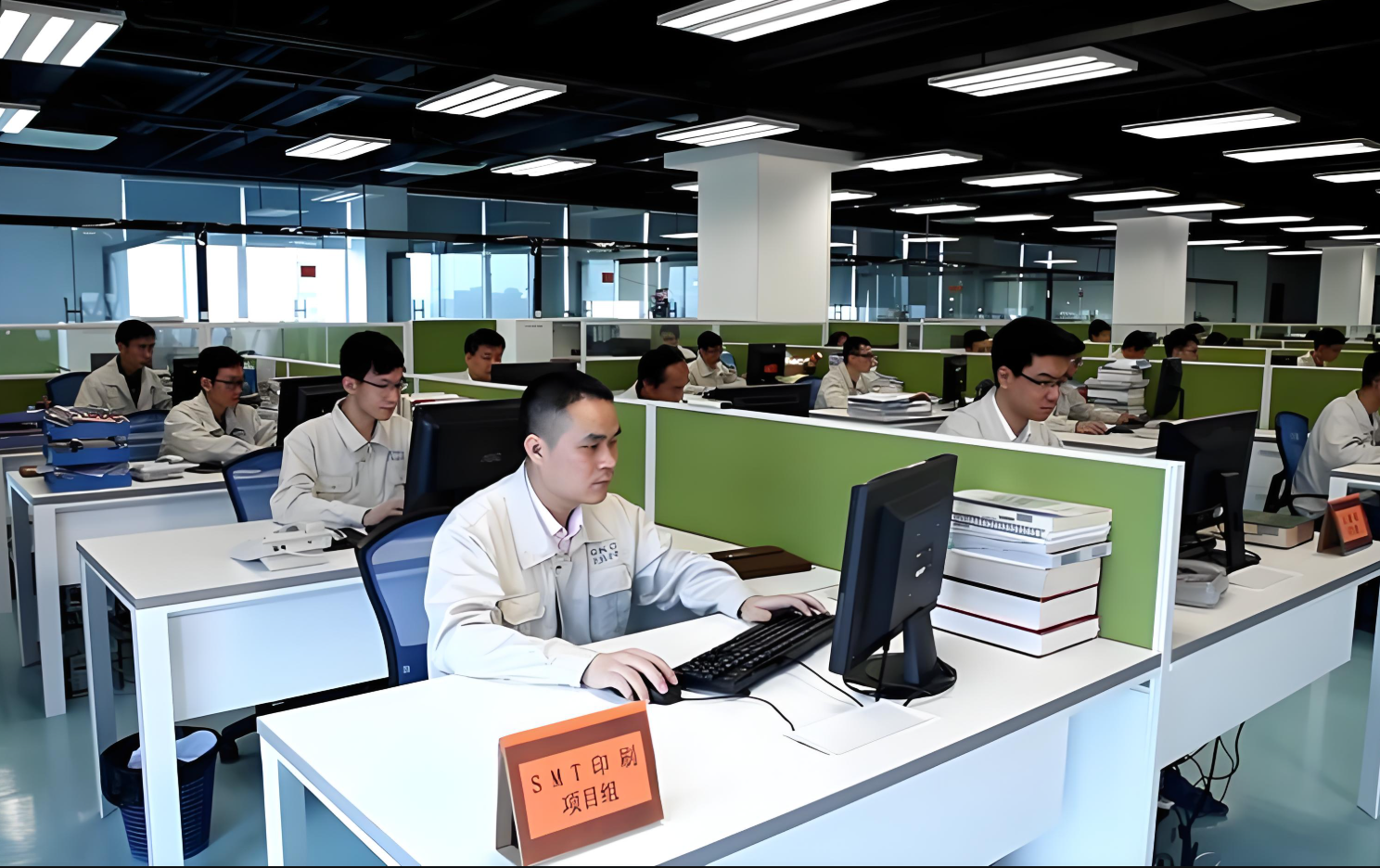
In the relentless pursuit of engineering perfection, industries from automotive to renewable energy face a common challenge: **how to test, measure, and control mechanical systems with unerring accuracy**. Enter the unsung heroes of motion control—hysteresis brakes, dynamometers, and motor testing systems. Torque sensing solutions ’t just meet expectations; they redefine them.
---
### The Silent Revolution: Hysteresis Technology Explained
At the heart of these systems lies **hysteresis**, a phenomenon where magnetic materials resist changes in magnetization. This principle powers devices like **hysteresis brakes** and **clutches**, which deliver smooth, wear-free torque control without physical contact. Imagine a braking system that never degrades, or a clutch that adjusts torque seamlessly—no friction, no heat buildup, just pure magnetic mastery.
For industries like aerospace, where reliability is non-negotiable, hysteresis brakes ensure precision in satellite deployment mechanisms. Meanwhile, electric vehicle manufacturers rely on hysteresis clutches to fine-tune power distribution in hybrid drivetrains. The result? Systems that last longer, perform better, and cost less to maintain.
---
### Dynamometers: Where Power Meets Precision
A motor’s true potential is only as good as the tools used to test it. **Hysteresis dynamometers** and **motor dynamometers** are the gatekeepers of performance validation. Unlike traditional load systems, hysteresis dynamometers apply torque electromagnetically, enabling ultra-precise load simulation.
Take wind turbine testing, for example. A hysteresis dynamometer can replicate the erratic forces of gusty winds on a turbine’s generator, allowing engineers to optimize energy output under real-world conditions. Similarly, in robotics, motor dynamometers validate servo motors’ responsiveness, ensuring robotic arms move with surgical accuracy.
But the magic doesn’t stop there. Modern **motor test systems** integrate AI-driven analytics, turning raw data into actionable insights. Picture a cloud-connected dynamometer that predicts motor failure months in advance—proactive maintenance that saves millions in downtime.
---
### The Clutch That Thinks: Hysteresis in Automation
In automated assembly lines, **hysteresis clutches** are the invisible conductors of orchestrated chaos. They regulate tension in conveyor belts, synchronize robotic arms, and even control the delicate spin of semiconductor wafer handlers. Their secret? A frictionless design that eliminates wear and tear.
A leading EV battery manufacturer recently swapped mechanical clutches for hysteresis models in their production line. The outcome? A 40% reduction in maintenance costs and a 15% boost in assembly speed. The clutch’s ability to adjust torque in milliseconds meant fewer errors and zero downtime—a game-changer for high-volume manufacturing.
---
### Beyond the Lab: Motor Test Equipment in the Real World
From Formula 1 teams to underwater drone developers, **motor test equipment** is the backbone of innovation. Consider the case of a marine engineering firm testing thrusters for autonomous submarines. Using a customized **motor test system**, they simulated ocean currents at depths of 3,000 meters, ensuring motors could withstand crushing pressures without faltering.
In the medical field, motor test systems validate the precision of surgical robots. A single miscalculation could spell disaster, but with dynamometers that measure torque down to 0.001 Nm, engineers guarantee flawless performance. It’s not just testing—it’s building trust in technology that saves lives.
---
### The Green Frontier: Hysteresis Tech in Renewable Energy
As the world pivots to renewables, hysteresis systems are stepping into the spotlight. Wind farms use hysteresis brakes to feather turbine blades during storms, preventing damage without mechanical wear. Solar trackers employ hysteresis clutches to adjust panel angles with sun-position algorithms, boosting energy harvest by 20%.
Even hydropower benefits. A Scandinavian energy company recently deployed hysteresis dynamometers to test tidal turbines in the North Sea’s harsh environment. The result? Turbines that generate power consistently, even in corrosive saltwater—proof that sustainability and durability can coexist.
---
### The Future Is Frictionless
What’s next for hysteresis technology? Think self-learning motor test systems that adapt to new prototypes in real time, or clutches embedded with IoT sensors for remote diagnostics. Researchers are even exploring hysteresis brakes for space elevators—yes, that’s a real concept—where zero maintenance is non-negotiable.

For engineers and innovators, the message is clear: **the era of friction-dependent systems is over**. Hysteresis brakes, dynamometers, and motor testing ecosystems aren’t just tools; they’re the foundation of tomorrow’s breakthroughs. Whether you’re building the next electric supercar or a microgrid for a remote village, these technologies ensure every watt, every rotation, and every millisecond counts.
---
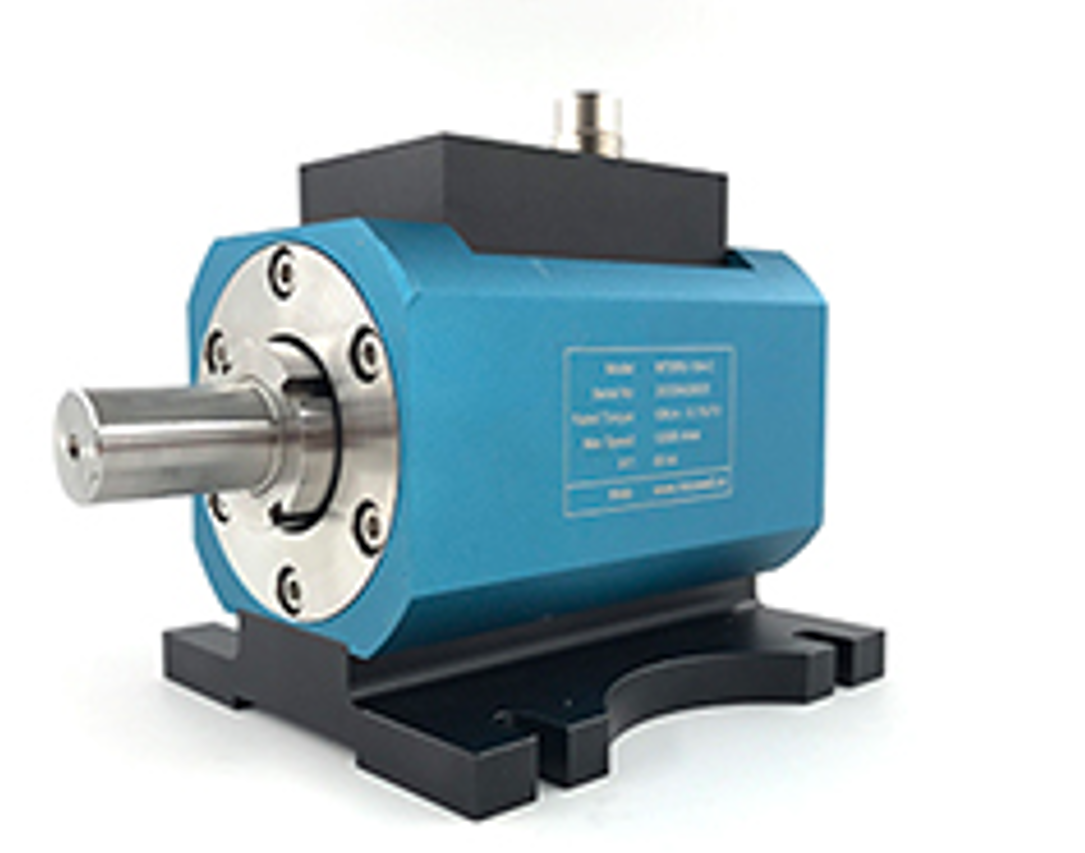
In a world hungry for efficiency and sustainability, hysteresis solutions aren’t optional—they’re essential. The question isn’t whether to adopt them, but how fast you can integrate them into your next project. After all, the future belongs to those who test, refine, and perfect. ⚙️🌍🚀